#06_LEGO_A
Vibration pattern optimization
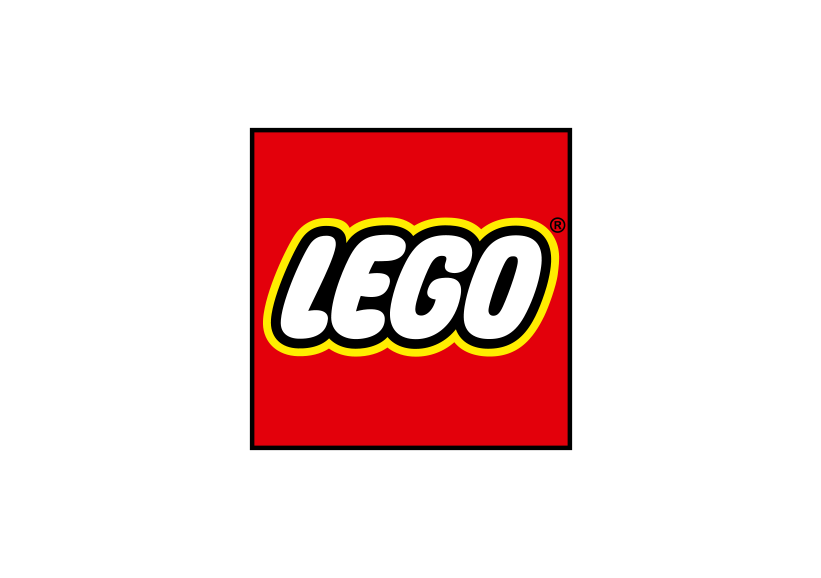
Context
At the LEGO group, our bricks are primarily created through the process of injection moulding. This ensures a precise and clean product after just one process. However, some of our elements require a post processing procedure, like printing, to ensure the highest level of quality and detail. To enable the printing process, it is crucial to constrain the elements in custom jigs, to guarantee that the prints are correctly aligned and printed. This process of constraining the elements is very challenging as almost all elements are produced and stored in large disorderly quantities in containers. A large part of handling our elements is segmenting them
Segmentation of elements consists of separating a bunch of elements into tangible portions (usually one). This can be achieved using a traditional bowl feeder, or a vibration table. Bowl feeders are extremely expensive, and custom made for each individual element, while flexible vibration feeders can handle multiple elements but hard to tune properly. For this case, we will focus on the usage of flexible vibration feeders to separate a volume of elements into correctly oriented elements.
Challenge
Develop a vibration pattern solution capable of aligning elements correctly on a vibration feeding table.
The objective is to always have elements ready for a robot to pick up with the shortest vibration time possible. The solution should be scalable to allow the introduction of new unknown elements.
The vibration solution can be tested on the supplied vibration testing station.
A vision application is supplied to validate the vibration solutions from The LEGO Group.
Tools, methods and materials
- Documentation of all the equipment
- Sample Python Code vibration table control
- Sample code to validate vibration solution
- Simplified 3D models of the elements
- The physical test platform
Ideal outcome for the company
A new general approach to tuning our vibration tables. Last year we tried to encompass the whole material handling process, this year we tried to start from scratch with focus on the feeding.