#10_UR_B
Optimized motion performance (physical)
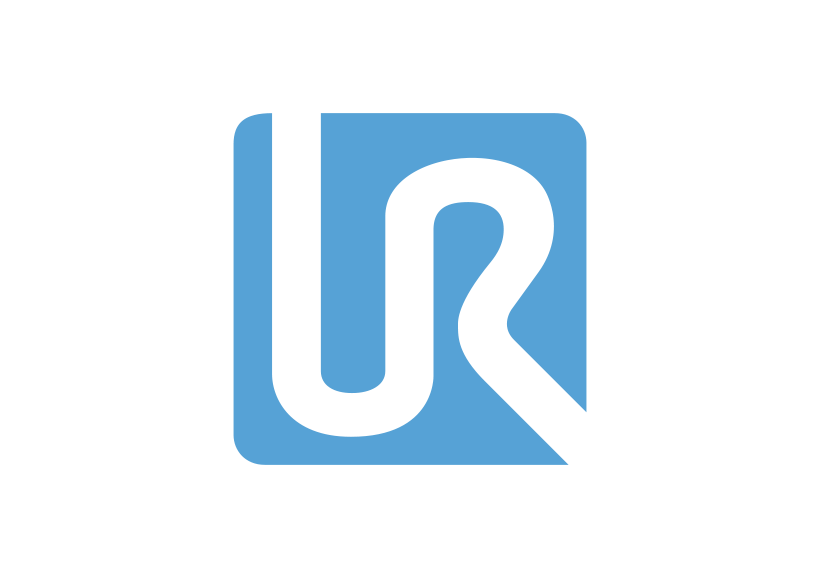
Case description
UR strives to improve the quality of their cobots by utilizing cutting-edge technologies such as machine learning/AI. UR is currently investigating if machine learning can be applied for optimizing the cycle time of common pick & place motions by using other path forms than linear paths in Cartesian or joint space and considering dynamic aspects such as payloads and gravity to yield sharp cycle times which are among the most important performance indicators delivered by robot manufacturers.
Challenge
Develop a real-time capable machine learning solution for pose-to-pose paths of a physical UR robot transporting a variety of payloads (known and unknown) which can positively impact cycle times for poses across the workspace.
To get the team started, consider the following:
- Can solutions exploit data from encoders and TCP accelerometer?
- Can solutions exploit data from force/torque sensor to estimate payload mass and inertia?
Keywords: Control optimization, velocity profile, acceleration profile
Tools, methods and materials
The challenge can be addressed with any machine learning tool allowing for generic time series data as input. The selection of tools and methods is left to the team. (Henrik)
From UR, the team will receive a UR robot arm and documentation how to command user-defined motions and how to access data from the force/torque sensor. In addition, UR will be available to discuss details of the challenge along the way.
Contact
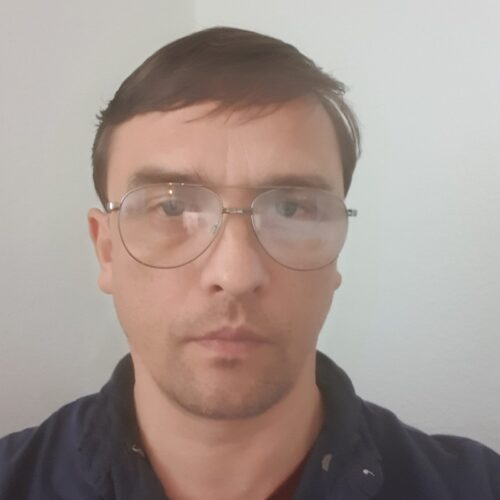
Leonid Paramonov
Universal RobotsLeonid Paramonov
Universal RobotsSenior software developer